Polyamides/PA/Nylon Rod, Nylon Sheet
About Nylon:
The most common engineering nylons are PA6 and PA66. Nylon stock shapes are produced by either extrusion or casting. The process is in part a determinant of the nylon properties of the end product. Modifiers are added to enhance desirable characteristics.
Advantages:
Nylon Rod and Nylon Sheet are tough, durable, general purpose engineering material with special grades for specialty applications. Typical application conditions would be medium speed and temperature in a rugged, abrasive, impact and high load environment.
Disadvantages:
Poor dimension stability, electrical and mechanical properties, may become affected by absorbing moisture or water, acidproof ability not good, can't dye with acid or touch overmuch acid, weak lightfastness, low endurance in pollution
Key Features:
-
Excellent bearing properties
-
High impact strength and toughness
-
Low power factor requirements
-
High wear resistance
-
Very good sliding properties
Applications:
-
High load bearings
-
Wear pads
-
Support and Guide wheels
-
Conveyor and Tension rollers
-
Wire rope sheaves
-
Buffer pads
-
Gears...
Nylon Products:
-
Extruded Nylon 6 (PA 6) - natural (white) / black:
Offers an optimal combination of mechanical strength, stiffness, toughness, mechanical damping properties and wear resistance. These properties, together with a favourable electrical insulating ability and a good chemical resistance make extruded nylon 6 a "general purpose" grade for mechanical construction and maintenance.
-
MC Nylon 6 (PA 6) - natural (ivory) / black:
Unmodified cast nylon 6 grade exhibiting characteristics which come very close to those of nylon 66. It combines high strength, stiffness and hardness with good creep and wear resistance, heat ageing properties and machinability.
-
MC Nylon 6 + oil filled (PA6 + oil) - green:
This internally lubricated cast nylon 6 is self-lubricating in the real meaning of the word. Oil filled MC nylon 6, especially developed for unlubricated, highly loaded and slowly moving parts applications, yields a considerable enlargement of the application possibilities of nylons. This because of its reduced coefficient of friction (up to -50%) and improved wear resistance (up to x 10).
-
Nylon 6 + MOS2 (PA6 + MoS²) - grey black:
The addition of MoS² renders this material somewhat stiffer, harder and dimensionally more stable than nylon 66, but results in some loss of impact strength. The nucleating effect of the molybdenum disulphide results into an improved crystalline structure enhancing bearing and wear properties.
-
Nylon 6+ GF30 (PA 6-GF30) - black:
when compared with virgin nylon 6, this 30% glass fibre reinforced and heat stabilised nylon grade offers increased strength, stiffness, creep resistance and dimensional stability whilst retaining an excellent wear resistance. It also allows higher max. service temperatures.
-
Nylon 66: this material with a higher mechanical strength, stiffness, heat and wear resistance than extruded nylon 6. It also has a better creep resistance but its impact strength and mechanical damping ability are reduced. Well suited for machining on automatic lathes.
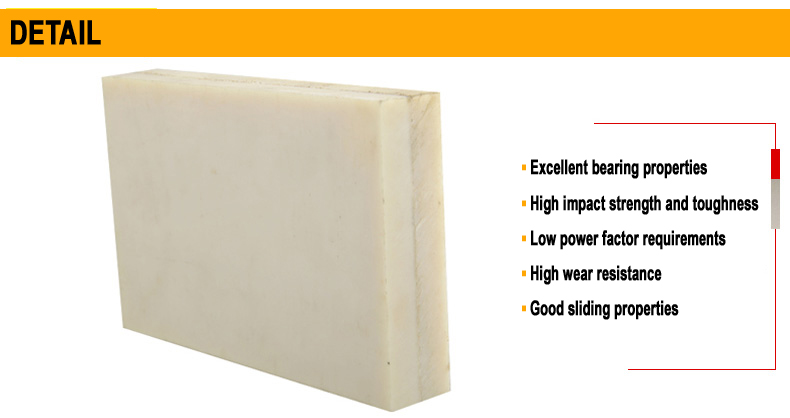
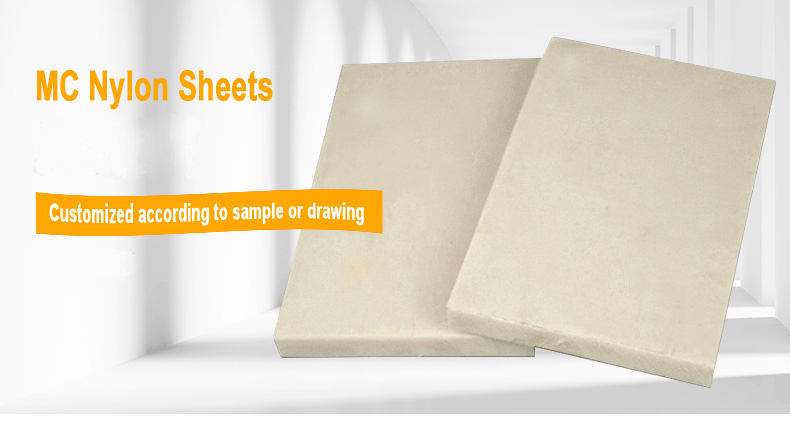
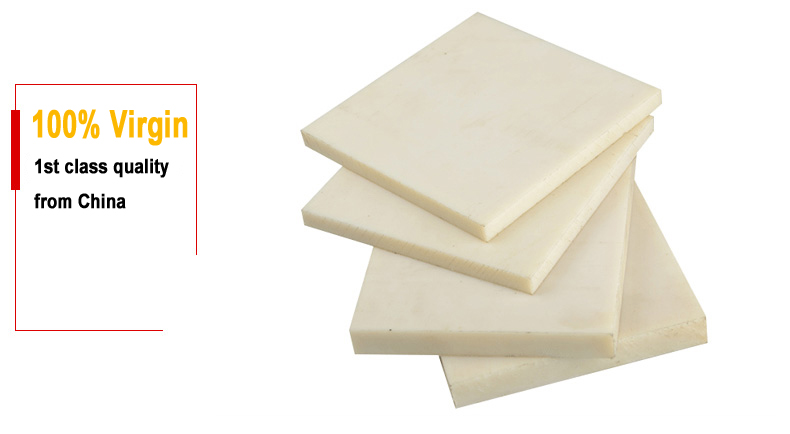
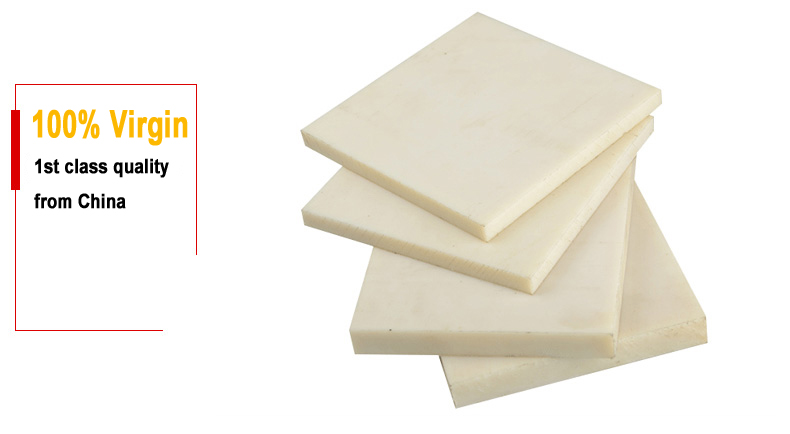
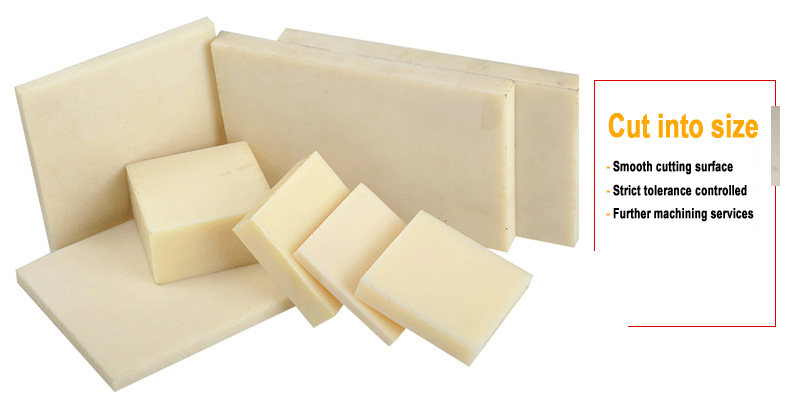
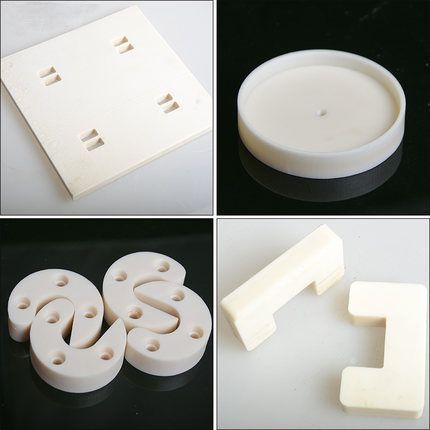