Plastic Gear for Mechanical Driving
plastic gears are mainly used for transmission, especially widely used in mechanical driving.
Which come with following features:
▪ Excellent bearing properties
▪ High impact strength and toughness
▪ Low power factor requirements
▪ High wear resistance
▪ Very good sliding properties
Types of plastic gear include: spur gear, helical gear, worm gear, crown gear, bevel gear, planetary gear, tooth box, damped gear, involute gear, cycloid gear, arc gear and other modulus gear, non standard grotesque gear, multi process complex glue gear, foreign standard low noise gear and so on.
The gear combination selection of various process parameters can effectively meet the requirements of design used, such as slow growth, energy conversion, timing, location of fixed and other functions.
The products are used in various industries such as micro motors, electronic products, auto parts, household appliances, office supplies, toys, handicrafts and so on. For example, in automobile rear view mirror, lamp regulator, timer, micro motor, reducer, printer, fax machine, camera, DVD core, paper shredder, copier, toy core, medical instrument, vacuum cleaner, automatic coffee machine and other products.
The causes of gear noise generation system mainly has the following several aspects:
1. Gear design parameters: improper selection, coincidence is too small, the tooth profile modification of improper or no modification, the gear box structure is not reasonable.
2. Gear processing: base joint error and tooth shape error is too large, side clearance is too large, rough surface and so on.
3. Gear and gear box assembly: eccentric contact, low precision, parallel shaft, shaft, bearing, bearing stiffness, rotary bearing accuracy is not high and the improper clearance.
4. Other aspects of the input torque. The fluctuation of load torque, the torsional vibration of shafting, the balance of motors and other transmission pairs, etc.
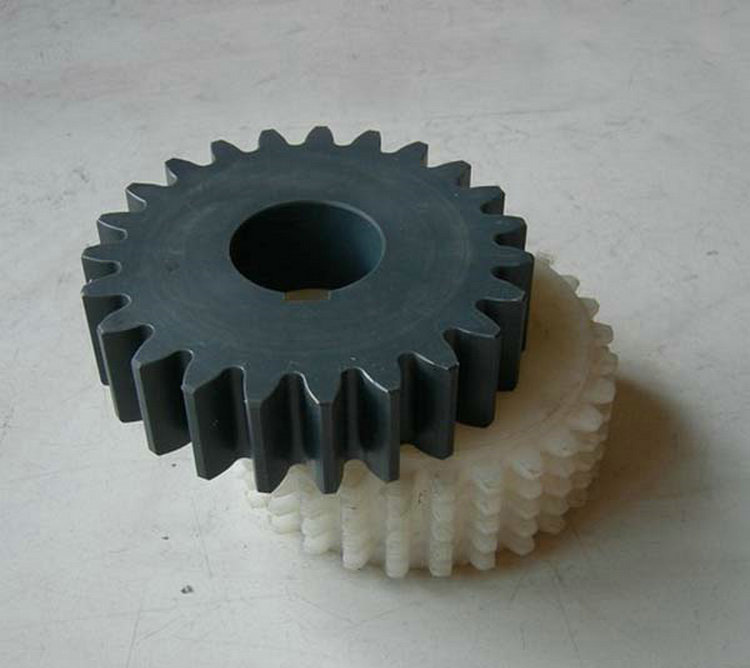